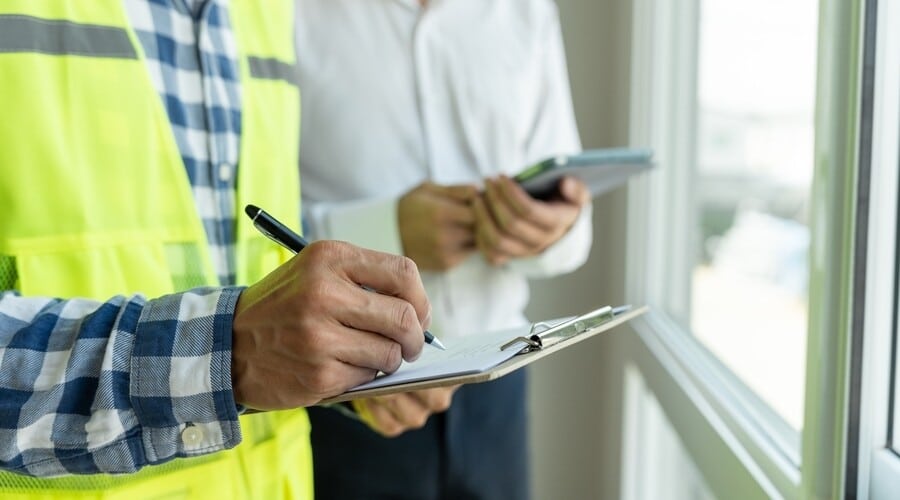
In building construction, quality assurance is an indispensable aspect that ensures the end product meets the highest standards of safety, functionality, and durability.
We'll delve into what quality assurance in building construction entails, how to manage it effectively, who bears the responsibility for maintaining impeccable construction quality, and why it’s so important.
Read on to learn what is quality assurance in building construction.
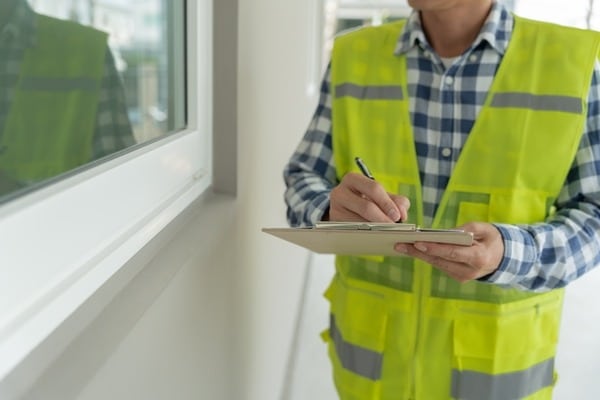
Quality assurance (QA) in construction ensures that projects consistently meet or exceed set quality standards.
What Is Quality Assurance in Building Construction?
Quality assurance (QA) in building construction is a systematic approach designed to guarantee that construction projects are executed in a manner that consistently meets or exceeds predetermined quality criteria.
It encompasses a series of processes, procedures, and protocols aimed at preventing defects, errors, and deviations throughout the construction lifecycle.
The primary goal of QA is to ensure that the completed building is structurally sound, safe for occupancy, and compliant with relevant regulations and industry standards.
Managing Quality Assurance in Building Construction
Effectively managing quality assurance in building construction involves a comprehensive strategy that begins at project inception and extends through design, construction, and project completion. Here's a breakdown of key steps:
-
Define Quality Objectives:
Start by establishing clear quality objectives for the project. These objectives should align with client expectations, industry standards, and regulatory requirements.
-
Document Quality Standards:
Document the specific quality standards, specifications, and codes that the project must adhere to. This documentation provides a clear reference point for all stakeholders.
-
Quality Planning:
Develop a Quality Management Plan (QMP) that outlines the processes, responsibilities, and procedures for maintaining quality throughout the project. The QMP should identify quality control checkpoints, inspections, and testing protocols.
-
Supplier and Contractor Selection:
Choose suppliers, contractors, and subcontractors with a proven track record of delivering quality work. Verify their qualifications, certifications, and adherence to industry standards.
-
Quality Control Inspections:
Implement a robust system of inspections and quality control measures at various stages of construction. This includes structural inspections, material testing, and compliance checks. Use Inspection Test Plan for specific projects.
-
Documentation and Reporting:
Maintain meticulous records of all quality-related activities, including inspection reports, test results, and any non-conformance issues. Report findings to relevant parties promptly.
-
Continuous Improvement:
Establish a culture of continuous improvement, where lessons learned from previous projects are applied to enhance quality processes.
Who Is Responsible for Quality Assurance in Building Construction?
Quality assurance in building construction is a shared responsibility involving multiple stakeholders:
Client
The client sets the project's quality expectations, approves design and material choices, and may engage a third-party quality assurance consultant.
Architects and Designers
Architects and designers play a pivotal role in ensuring that the building's design meets quality standards and codes.
Builder and Subcontractor
Ultimately the builder is responsible for overall quality control. This is then passed onto the subcontractors who provide quality control on what they provide to the builder. There is an ITP for each subcontractor, for example, plumber, electrician and the like. There isn’t an ITP for a builder, it’s the trades that need to check their work and provide a quality product. The builder collects the ITPs from the subcontractors. All Builder Assist ITPs are trade related, have a look at the types of trades.
Quality Control Inspectors
These professionals conduct inspections and assessments to verify compliance with quality standards and project requirements.
Third-party Consultants
In some cases, clients hire independent consultants or quality assurance experts to oversee and report on the project's quality performance.
Why Quality Assurance in Building Construction Is Paramount
Quality assurance in building construction holds immense significance due to its far-reaching impacts on the safety, longevity, and overall success of construction projects (and companies).
Here are compelling reasons why quality assurance is indispensable in the construction industry:
Safety First
The safety of occupants and users is paramount in any construction project. Quality assurance ensures that structural elements, electrical systems, plumbing, and other crucial components are installed correctly and function safely. This proactive approach minimises the risk of accidents, injuries, and structural failures that could result from subpar workmanship.
Long-Term Durability
High-quality construction materials and workmanship translate to long-term durability. Buildings constructed with precision and attention to detail are less likely to require frequent repairs or premature replacements. This not only reduces maintenance costs but also enhances the building's overall lifespan.
Compliance with Regulations
Building codes, regulations, and industry standards are in place to safeguard public safety and health. Quality assurance ensures that a project complies with these regulations, minimising the risk of legal issues, fines, or the need for costly retrofits to meet code requirements.
Client Satisfaction
Meeting or exceeding client expectations is essential for maintaining a positive reputation in the construction industry. Quality assurance ensures that the finished product aligns with the client's vision, enhancing client satisfaction and potentially leading to future collaborations and referrals.
Cost Savings
While investing in quality assurance may seem like an additional cost, it often results in substantial long-term savings. Preventing defects and errors during construction minimises the need for costly rework, which can be a significant drain on project budgets and schedules.
Risk Mitigation
Comprehensive quality assurance helps identify and address potential risks early in the construction process. This proactive risk management approach reduces the likelihood of unexpected issues arising during or after construction, which can be financially and logistically challenging to rectify.
Enhanced Market Competitiveness
Construction firms known for their commitment to quality assurance are more competitive in the market. A strong track record of delivering high-quality projects can differentiate a company and attract clients seeking reliability and excellence.
Public Image
High-profile construction projects often receive public scrutiny. Ensuring quality not only meets legal and ethical obligations but also safeguards a company's public image. Reputation is a valuable asset in the construction industry.
Insurance and Liability
Quality assurance can positively impact insurance costs and liability concerns. A well-documented commitment to quality and safety practices may lead to lower insurance premiums and reduced liability exposure.
In conclusion, quality assurance in building construction is a multifaceted process that demands meticulous planning, careful execution, and continuous monitoring.
It is the collective responsibility of clients, architects, builders, subcontractors, and quality control inspectors to ensure that every construction project delivers a high-quality, safe, and compliant end result.
By prioritising quality at every stage of a construction project, the industry upholds its commitment to excellence, safety, and client satisfaction, ultimately reaping the numerous benefits of sound quality assurance practices.
If you require quality assurance documentation like Inspection Test Plans or Quality Management Plans, Builder Assist have developed industry-leading trade-specific templates that adhere to Australian Standards. All Builder Assist templates adhere to the ISO 9001 standard for quality management.
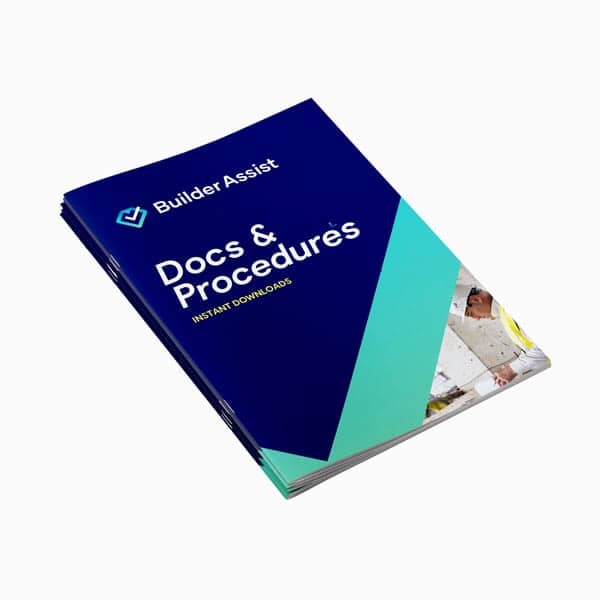
Construction ITP - Inspection Test Plans (ITP's)
These Construction Inspection Test Plans (ITPs) are specifically prepared for each building trade to provide support with quality assurance in the workplace.
A construction ITP assists to create a product that meets customer needs, expectations and requirements. And that's why you need one.
An ITP, or Inspection Test Plan, is a vital planning tool that delivers an effective solution to the when what and how of inspections for a project. It provides structure and procedural alignment. In addition, an ITP sets up the important preplanning to ensure your outcomes meet the necessary industry or regulatory standards. Here's a great resource for builders - the ITP Construction template pack.