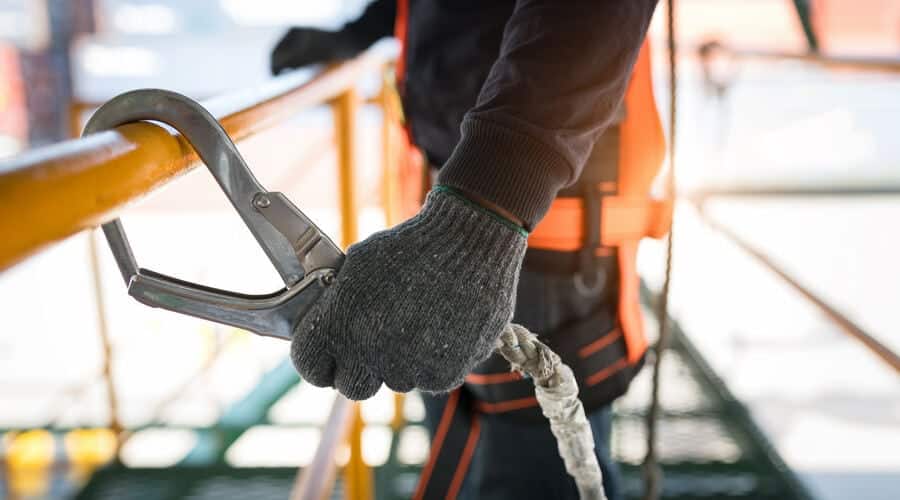
Encouraging and growing safe work practices will save you money, reduce project delays and improve the overall workplace health and safety of a construction site.
A compliant construction company will have Safe Work Method Statement (SWMS) documentation and other WHS procedures implemented across their worksites. However, this doesn’t guarantee all staff and workers will adopt safe work practices.
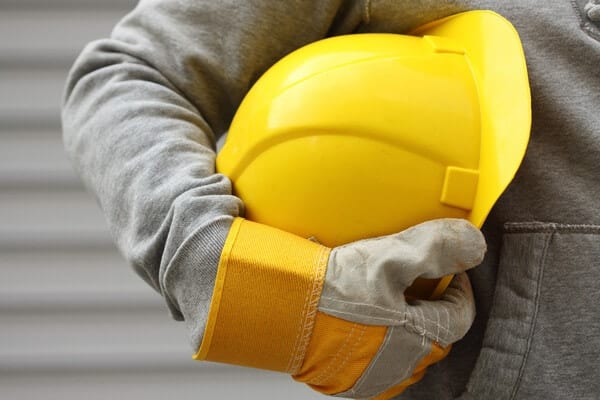
Safe work practices filter from the top down. Demonstrate your commitment and workers will follow your lead.
Here are our top tips for cultivating and nurturing safe work practices on worksites:
1. Prioritising Employee Safety
A focus on safety should be high on the priority list. Expenses, turnaround times and deadlines come after this. Employees are the highest-value business asset - without them, there is no work.
Show this to your employees by voicing your commitment to keeping them safe. This instantly drives deeper employee engagement; the key to every business’ success.
2. Safe Work Practices and Regular Training
Intensive and regular training is a sure-fire way to encourage safe work practices. It reiterates your interest in your employees’ safety and wellbeing.
Training should be ongoing. It brings your teams closer, enables them to interact with each other, and motivates them to work together. Furthermore, it encourages long-term retention.
3. Encourage Involvement
Encourage staff to elect a multi-hierarchy committee to handle all safety matters. This committee is responsible for driving reviews, updates and site-safety plans.
Include corrective plans, as well as preventative plans, and engage with employees for input into these plans (via the committee).
The committee, and management, must ensure all employees have knowledge of, and access to these plans.
Encourage feedback on concerns relating to safety and ensure that action is taken. If employees believe that you truly take safety seriously, they will too.
4. Safe Work Practices and Accountability
Ensure all employees know that THEY are accountable for safety. Not just their team leaders, supervisors or managers. Make is clear that you view unsafe work processes as a threat to the safety of entire team.
Safety plans, SWMS and accident plans should be made available, and explained to all workers. As well as the ramifications for failing to follow these practices.
Encourage open feedback. Including safety issues, accidents that were avoided, or anomalies found on site.
Encourage a culture where all workers feel confident to bring up safety issues and risks. Workers should never be shamed or punished for talking about safety.
5. Rewards and Discipline
Incentivise good safety behaviour across your staff pool! Acknowledged and reward practices such as:
- adhering to SWMS,
- regular attendance of safety meetings,
- consistent use of PPE,
- reporting incidents, and
- providing safety suggestions.
Avoid incentivising accident-free weeks. This can lead to a reduction in incident reporting, which is not the end-goal!
6. Inspections and Meetings
A safety inspection should occur at the beginning and end of each day. This can pick up any oversights, such as misplaced tools or damage to materials or equipment.
Start the working day with a quick safety focus meeting and list the day’s tasks and their related SWMS. Discuss any feedback received from workers. Don’t forget to give praise where it's due.
Ad hoc daily inspections should also be implemented to pick up any risks to safety.
Safe work practices filter from the top down. Show your commitment to achieving this and your workers will naturally follow your lead.
Safety Documentation
Builder Assist have a number of safety documentation resources available to building industry trades. Start implementing safe work practices today!
To find out what other documentation, procedures and checklists you need in your trade, head to Tradespeople Documentation for a full list or get in touch with the Builder Assist team today!
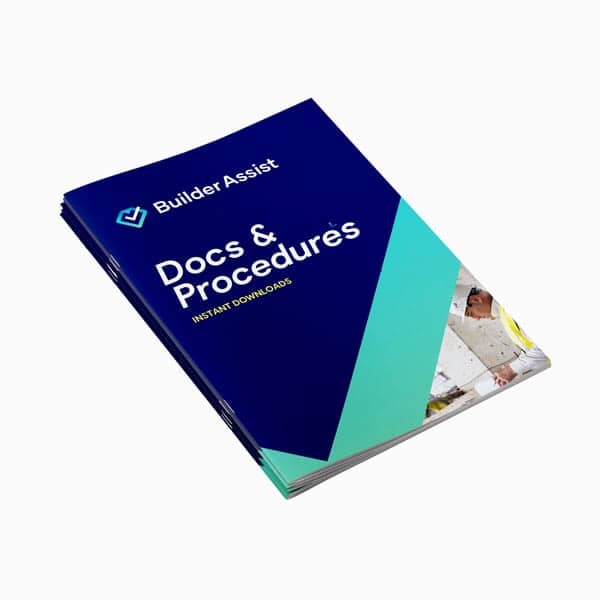
Safety Management Plans (WHS)
Specifically designed for each trade starting up a business, these Work Health Safety Management Plans or WHS Management Plans, provide support with the management of Work Health & Safety in the workplace. Also referred to as Occupational Health & Safety (OH&S) the material provided in this section will assist with WHS/OHS management and training requirements for the workplace.