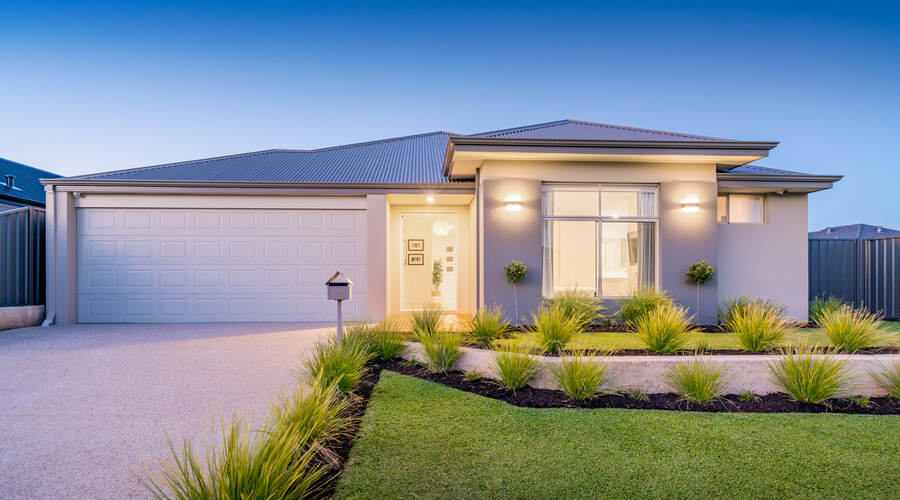
Maintaining high standards of safety and quality in every building project is essential for upholding your company’s reputation and ensuring the production of superior products.
One critical concept that plays a significant role in ensuring these standards is non-conformance.
But what exactly does non-conformance mean in the context of the building industry? And, why is it so important to address these issues promptly? We cover this topic in detail and explore its implications for builders and tradespeople.
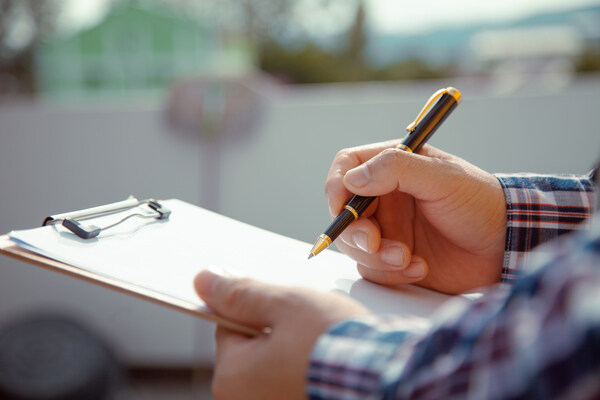
Maintaining high standards of safety and quality in every building project is essential for upholding your company’s reputation.
What is Non-Conformance?
Non-conformance refers to any deviation from the established standards, specifications, or regulations in the construction process. This could include using incorrect materials, failing to follow design plans, or not complying with safety protocols. Essentially, it highlights any instance where the actual work does not meet the expected criteria.
Types
There are two main types of non-conformance: minor and major. Minor refers to small deviations that do not significantly impact the project's overall quality or safety. Examples include minor inaccuracies in measurements or slight deviations from material specifications.
Major, on the other hand, involves significant deviations that can affect the structural integrity, safety, or functionality of the building. This includes major design flaws, using substandard materials, or failing to adhere to critical safety protocols.
Importance of Identification
Recognising and addressing non-conformance is crucial for several reasons. Firstly, it helps maintain the quality and safety of the construction project. Ignoring it can lead to severe consequences, including structural failures, safety hazards, and costly repairs.
Secondly, addressing the issue ensures compliance with industry standards and regulations. This is vital for avoiding legal issues and maintaining a good reputation in the industry. Clients and regulatory bodies expect construction companies to adhere to the highest standards of quality and safety.
How to Identify Non-Conformance
Identification involves regular inspections and quality checks throughout the construction process. This includes comparing the actual work against the design plans, material specifications, and safety standards. Using Quality Management Plans (QMPs) and Inspection Test Plans (ITPs) can help ensure that all aspects of the project are reviewed thoroughly.
For more information about QMPs, head to our blog: What is a QMP? Or, for more information about ITPs visit our blog: What does ITP mean in construction?
Addressing The Issue
Addressing non-conformance involves several steps. First, it is essential to document the issue. This includes detailing the nature of the deviation, its location, and the affected components. Documentation helps track the issue and provides a basis for corrective actions.
Next, a root cause analysis should be conducted to determine the underlying reasons. This helps identify potential weaknesses in the construction process and prevent similar issues in the future.
Finally, corrective actions should be implemented. This could involve reworking the affected components, replacing materials, or modifying the design. It is crucial to ensure that all corrective actions comply with the established standards and regulations.
Resources
Builder Assist provides two main resources. A Non-conformance Report Register and a Non-conformance Report Notice. Whenever a system deficiency is identified, typically following an audit or inspection, a “Non-Conformance Report Notice” should be completed and issued to the responsible party. This report outlines the identified deficiency, and the proposed corrective actions, and includes verification upon completion.
When a Report Notice is completed, it is then recorded in the “Non-Conformance Report Register” to maintain a comprehensive record of all Non-Conformance Reports issued on site.
Prevention
Preventing non-conformance requires a proactive approach. This includes thorough planning, proper training, and regular monitoring of the construction process. It is essential to establish clear standards and procedures for all aspects of the project. These can be easily set out in your Quality Management Plan.
Conclusion
Non-conformance is a critical issue in the building industry that can significantly impact the quality and safety of construction projects. By understanding what it means and why it’s essential to address it, builders and tradespeople can take proactive steps to ensure compliance with industry standards and regulations. Regular inspections and proper training are key strategies for identifying and preventing non-conformance, ultimately leading to successful and safe construction projects.